Wilmer Pacheo, Ph.D., fue el encargado de la ponencia sobre “Tecnologias fabricación de alimentos” durante el LPN 2021.
El costo del alimento representa entre 60 y 70% de los costos totales en producción avícola. Cada uno de los pasos en la elaboración de alimento balanceado (recepción de ingredientes, molienda, pesado y dosificación, mezclado, peletizado, enfriamiento y embolsado) puede tener un efecto positivo o negativo en el desempeño de las aves.
La recepción es la primera línea de defensa dentro de un programa de control de calidad ya que la calidad de los ingredientes no se puede mejorar después de la recepción e ingredientes de baja calidad o con mayor contenido de humedad son más difíciles de manejar durante almacenamiento y procesamiento.
El muestreo y la evaluación de las características físicas y químicas de los ingredientes antes de la descarga y el monitoreo del nivel de micotoxinas es esencial para la producción de alimentos de calidad.
MOLIENDA
La mayoría de los ingredientes usados en dietas para aves requieren de algún tipo de molienda. La molienda se logra usando molinos de martillos o molinos de rodillos. Los molinos de martillo son populares en dietas peletizadas debido a su capacidad para producir un amplio tamaño de partículas y a su fácil operación.
Los molinos de rodillos son normalmente usados en dietas alimentadas en harina ya que producen un tamaño de partícula más uniforme y con mejores características de flujo comparado a los molinos de martillo.
La molienda aumenta el área superficial de los ingredientes, reduce la segregación de nutrientes durante el transporte, aumenta la penetración de vapor y humedad durante el acondicionamiento y la aglomeración durante peletizado.
El aumento en el área superficial permite que las enzimas digestivas tengan un mejor acceso a sus sustratos, lo que conduce a una mayor digestibilidad de los nutrientes. Sin embargo, molienda muy fina (<400 µm) puede ocasionar pérdidas de humedad, causar problemas de flujo de ingredientes y alimentos en harina e incrementar la tasa de pasaje a través del intestino de las aves, lo que puede reducir la digestibilidad de nutrientes y ocasionar problemas de salud intestinal.
A diferencia de los mamíferos, las aves tienen un tracto intestinal más corto, lo cual resulta beneficioso en condiciones normales ya que el costo energético de volar incrementa con el peso del tracto gastrointestinal (CaviedesVidal et al., 2007). La inclusión de partículas gruesas incrementa el desarrollo de la molleja.
De acuerdo con Ferket (2000), una molleja bien desarrollada mejora la motilidad del intestino, promueve una mejor digestión y absorción de nutrientes y reduce el riesgo de coccidiosis y otras enfermedades entéricas. Adicionalmente, la incorporación de partículas gruesas puede ayudar a modificar la microflora intestinal a través de un incremento en el número de bacterias benéficas y/o una reducción de bacterias patógenas (Gabriel et al., 2003).
Partículas gruesas incrementan el peristaltismo reverso entre la molleja y el proventrículo, lo que incrementa la digestión de proteínas, emulsificación de grasas y reduce el pH de la molleja, lo cual puede inactivar bacterias patógenas antes que ingresen al intestino delgado (Engberg et al., 2002; Bjerrum et al., 2005).
Ya que el tamaño de partícula puede influenciar el desempeño y la digestibilidad de nutrientes, se debe hacer un análisis del tamaño de partícula al menos semanalmente, después de realizar cualquier mantenimiento preventivo y/o correctivo en el equipo de molienda como ser cambiar cribas, cambiar martillos/ rodillos o cuando las características del maíz cambian (p.ej. nueva cosecha de maíz).
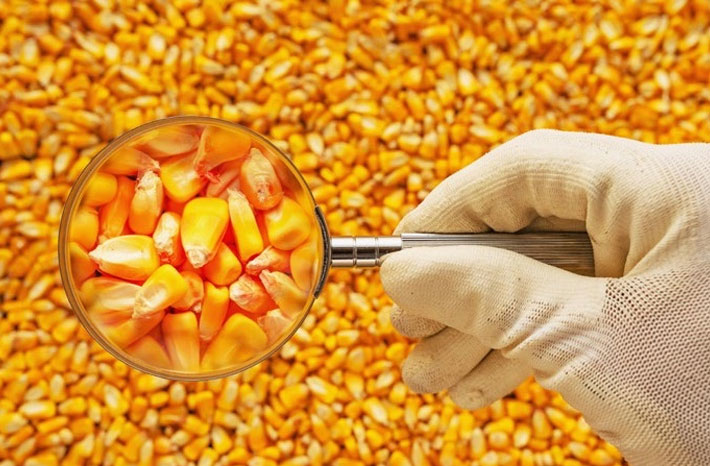
PESADO Y MEZCLADO
El principal objetivo del pesado y mezclado es producir alimentos en los que los nutrientes se distribuyan uniformemente en el menor tiempo posible. El proceso de mezclado es simple y consiste en transferir los ingredientes a una mezcladora, mezclarlos durante un tiempo de mezcla seco, agregar líquidos y luego mezclarlos durante un tiempo de mezclado húmedo.
Aunque el mezclado es simple, durante el mezclado pueden ocurrir problemas tales como: sobrellenado de la mezcladora debido a cambios en la densidad de los ingredientes, acumulación de residuos en las cintas o paletas, orden incorrecto en la adición de los ingredientes, listones rotos, entre otros. Los problemas de mezclado se pueden identificar y corregir mediante un mantenimiento preventivo regular, inspecciones visuales y pruebas de uniformidad.
La uniformidad de la mezcladora debe evaluarse después de la instalación y al menos una vez al año. La uniformidad del mezclado se estima midiendo el coeficiente de variación (CV) de un nutriente o ingrediente con un nivel de inclusión menor al 0.5%. Algunos de los ingredientes/ nutrientes utilizados comúnmente incluyen: cloruro, micro trazadores o aminoácidos. Por lo general, se recomienda un CV del 10% o menos.
En general, la uniformidad del mezclado aumenta a medida que se aumenta el tiempo de mezclado. Para medir el CV se deben tomar muestras representativas directamente del mezclador, tolva de compensación de 10 ubicaciones preseleccionadas o durante la transferencia del alimento de la tolva de compensación al elevador (se deben de tomar las muestras a intervalos uniformes y muestrear todo el lote).
El CV se calcula dividiendo la desviación estándar por la media aritmética de las muestras analizadas y luego multiplicando el valor obtenido por 100. Herrman y Benhke (1994) proporcionaron pautas para interpretar y corregir problemas relacionados con la uniformidad de mezclado (Tabla 1). Es importante re-evaluar la uniformidad después de realizar una acción correctiva para garantizar que el problema de uniformidad fue corregido.
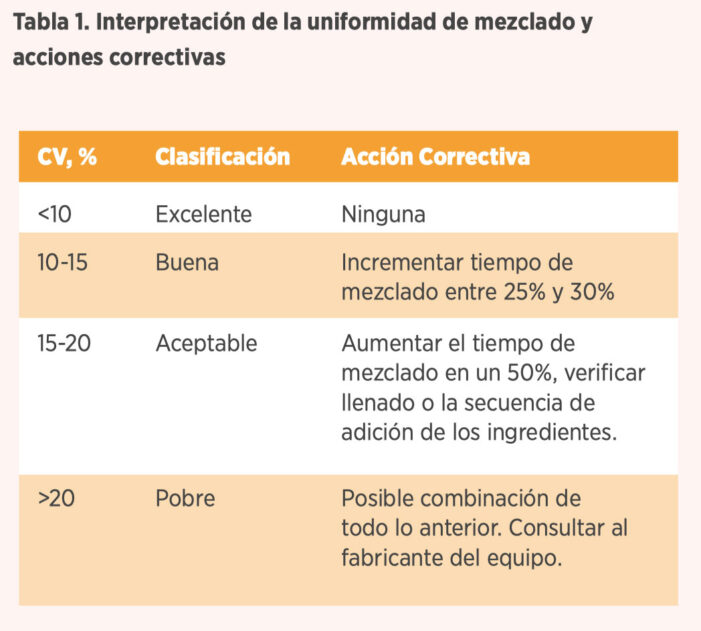
PELETIZADO
El peletizado es un proceso durante el cual ingredientes individuales o harinas se aglomeran utilizando vapor, humedad y presión (Massuquetto et al., 2020). El peletizado reduce el desperdicio y la alimentación selectiva y mejora la ganancia diaria, índice de conversión alimenticia, uniformidad de la parvada y digestibilidad de nutrientes (Behnke, 1994; McKinney and Teeter, 2004).
La calidad de pellet es la capacidad de los pellets para resistir desintegración y abrasión durante el transporte (Briggs et al., 1999). La calidad de pellet puede tener un impacto significativo en el rendimiento de las aves, índice de conversión alimenticia y digestibilidad de nutrientes (Buchanan et al., 2010; Lilly et al., 2011).
La calidad del alimento peletizado es influenciada por la formulación, tamaño de partícula, temperatura y tiempo de retención durante el acondicionamiento, especificación de la matriz de la peletizadora (relación entre el espesor de la matriz y el diámetro de los orificios), así como secado y enfriado (Behnke, 1994). Sin embargo, el porcentaje de grasa adicionada en la mezcladora y la tasa de producción también pueden influir en la calidad del alimento peletizado.
La harina entra a un alimentador el cual, por medio de un motor de velocidad variable, regula el flujo de alimento usando un tornillo sin fin. El acondicionamiento es el primer paso antes del peletizado donde la harina se mezcla con vapor y se calienta e hidrata lo que ayuda a extraer aglutinantes naturales y mejora la aglomeración durante el peletizado. El tiempo de retención en el acondicionador es importante para que haya una buena migración de calor y humedad al centro de las partículas.
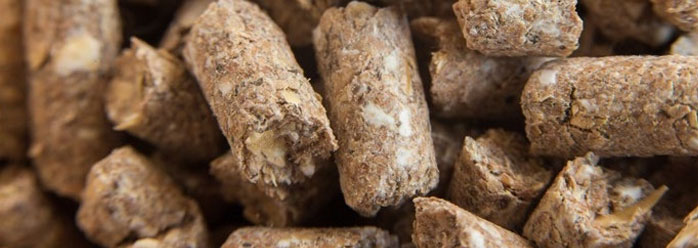
El tiempo de retención está influenciado por el diseño del acondicionador (simple, doble, triple), el ángulo de las paletas y la velocidad del acondicionador. Por lo general, a medida que aumenta la temperatura de acondicionamiento y el tiempo de retención en el acondicionador se mejora la calidad del alimento peletizado. Sin embargo, altas temperaturas durante el acondicionamiento (>90°C) pueden reducir la disponibilidad de vitaminas, reducir digestibilidad de aminoácidos y desactivar enzimas exógenas.
La temperatura de acondicionamiento óptima no es un “valor fijo” y está influenciada por varios factores, como ser: tiempo de retención en el acondicionador, humedad inicial de la harina, porcentaje de grasa agregada en la mezcladora entre otros.
Inmediatamente después del proceso de acondicionamiento, la harina es transportada a la cámara de peletizado donde se forman los pellets usando una matriz anular giratoria con múltiples orificios cilíndricos.
Dado que el proceso de acondicionamiento no es suficientemente para permitir la hidratación completa de la harina, se forman enlaces húmedos entre partículas y se produce gelatinización del almidón en la superficie del pellet, lo que contribuye a la dureza del pellet (Thomas and van der Poel, 2020). Matrices con una mayor relación de compresión (medida por la relación entre el espesor efectivo y el diámetro del orificio) tienen un impacto positivo en la calidad del pellet al aumentar el grado de compactación entre partículas y la gelatinización del almidón en la superficie de los pellets. Sin embargo, a medida que se incrementa la relación de compresión de la matriz, se reduce la tasa de producción.
Los pellets salen de la cámara de peletizado calientes, húmedos, frágiles y deben enfriarse y secarse gradualmente para un almacenamiento seguro. Durante el enfriamiento, componentes solubles se recristalizan y se forman puentes sólidos entre partículas (Thomas and van der Poel, 2020).
El flujo de aire y el tiempo de retención en el enfriador determinan la temperatura y humedad del alimento finalizado. Un alto flujo de aire en combinación con un tiempo de retención bajo puede causar grietas en la superficie de los pellets y aumentar su susceptibilidad a abrasión, lo que puede afectar negativamente su durabilidad. Además, si la superficie de los pellets se enfría rápidamente esto puede evitar la migración de humedad del centro del pellet, lo que puede producir pellets húmedos, frágiles y con menor densidad de nutrientes.
Como regla general, los pellets que salen del enfriador no deben estar más de 5°C por encima de la temperatura ambiente y tener ± 0.5% de la humedad del alimento mezclado. El aumento de la profundidad de la cama de pellets aumenta el tiempo de contacto entre el aire y los pellets y mejora el secado.
De hecho, cambios en la temperatura de acondicionamiento o en la tasa de producción ameritan cambios en el enfriado. Por ejemplo, un aumento de la tasa de producción puede reducir el tiempo de retención en el enfriador y aumentar la humedad y la temperatura del alimento peletizado.
Estos dos objetivos no suelen ser complementarios y, en ocasiones, se excluyen mutuamente. Por lo tanto, el trabajo en equipo es importante para lograr los objetivos de producción sin comprometer la calidad del alimento.
Los empleados deben recibir capacitación constante y el equipo recibir mantenimiento preventivo y correctivo para mantener todo el equipo de molienda, mezclado y peletizado funcionando de manera eficiente. Las estrategias de manejo deben ajustarse de acuerdo a cada situación.
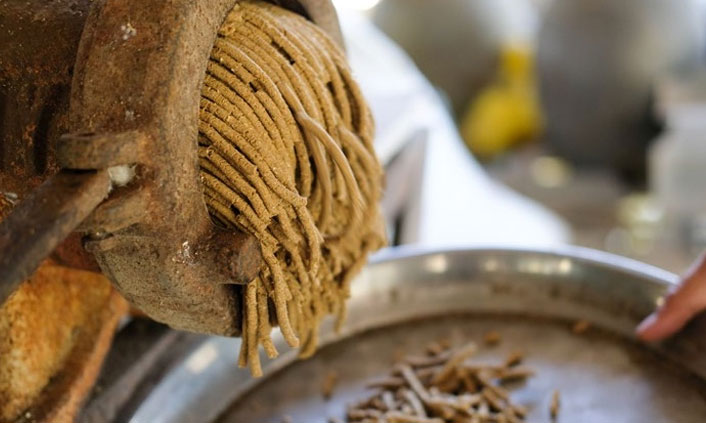
Por ejemplo, si la calidad del pellet es superior al 90%, pero los empleados trabajan 6 o 7 días a la semana para lograr los objetivos de producción, sin dejar tiempo para hacer mantenimiento; aumentar la cantidad de grasa agregada en el mezclador en un 0.25% (por ejemplo, 0.50 a 0.75%) o usar una matriz más delgada (1½ ”en lugar de 1¾”) puede ayudar a aumentar la tasa de producción sin reducir significativamente la calidad del alimento peletizado. Si la calidad del alimento peletizado es marginal (< 75% PDI), pero la planta de concentrados únicamente opera 4 a 5 días a la semana; reducir la cantidad de grasa en la mezcladora puede mejorar la calidad del alimento peletizado.
Para mantener un buen equilibrio entre objetivos de producción, calidad del alimento y el rendimiento de las aves, es importante entender la importancia del tamaño de las partículas, pesado y mezclado, acondicionamiento, peletizado y enfriamiento en la calidad del alimento. La producción eficiente de carne y huevos requiere un enfoque integrado y, por lo tanto, cada área debe gestionarse de manera eficiente.
REFERENCIAS
Behnke, K. C. 1994. Factors affecting pellet quality. Maryland Nutr. Conf, Dept. of Poultry Science and Animal Science, College of Agriculture, Univ. of Maryland, College Park.
Briggs, J. L., D. E. Maier, B. A. Watkins, and K. C. Behnke. 1999. Effect of ingredients and processing parameters on pellet quality. Poult. Sci. 78:1464-1471.
Buchanan, N. P., K. G. S. Lilly, and J. S. Moritz. 2010. The effects of altering diet formulation and manufacturing technique on pellet quality. J. Appl. Poult. Res. 19:112-120.
Bjerrum, L., K. Pedersen, and R.M. Engberg. 2005. The influence of whole wheat feeding on Salmonella infection and gut flora composition in broilers. Avian Dis. 49(1):9-15.
Caviedes-Vidal, E., T.J. McWroter, S.R. Lavin, J.G. Chediack, C.R. Tracy, and W.H. Karasov. 2007. The digestive adaptation of flying vertebrates: High intestinal paracelullar absorption compensates for smaller guts. Proc. Natl. Acad. Sci. USA 104(48):19132-19137.
Engberg, R.M., M.S. Hedemann, and B.B. Jensen. 2002. The influence of grinding and pelleting of feed on the microbial composition and activity in the digestive tract of broiler chickens. Br. Poult. Sci. 43(4):569-579.
Ferket, P. 2000. Feeding whole grains to poultry improves gut health. Feedstuffs 72:12-14.
Gabriel, I., S. Mallet, M. Leconte, G. Fort, and M. Naciri. 2003. Effects of whole wheat feeding on the development of coccidial infection in broiler chickens. Poult. Sci. 82(11):1668-1676.
Herrman, T., and K. C. Behnke. 1994. Testing mixer performance. Feed Manufacturing. Kansas State University. MF-1172.
Lilly, K. G. S., C. K. Gehring, K. R. Beaman, P. J. Turk, M. Sperow, and J. S. Moritz. 2011. Examining the relationships between pellet quality, broiler performance, and bird sex. J. Appl. Poult. Res. 20:231-239.
Massuquetto, A.; Panisson, J.C.; Schramm, V.G.; Surek, D.; Krabbe, E.L.; Maiorka, A. Effects of feed form and energy levels on growth performance, carcass yield and nutrient digestibility in broilers. Animal 2020, 14, 1139–1146.
McKinney, L. J., and R. G. Teeter. Predicting effective caloric value of nonnutritive factors: I. Pellet quality and II. Prediction of consequential formulation dead zones. Poult. Sci. 83:1165-1174.
Thomas, M., and A. F. B. van der Poel. 2020. Fundamental factors in feed manufacturing: Towards a unifying conditioning/pelleting framework. Anim. Feed Sci. Technol. 268:1-8.